
The 3D printer is built for serialized manufacturing, with dual 1000W lasers that allow large parts to be manufactured quickly, and two rotating build modules which allow for one build to take place while another is being set up. (800mm x 400mm x 500mm), assemblies can be designed and printed as a single piece. The X-Line 2000R model is a large format direct metal laser sintering machine (DMLS) which, due to its large build volume, is able to additively manufacture large scale parts. The GE Additives Concept Laser X Line 2000R 3D printer.
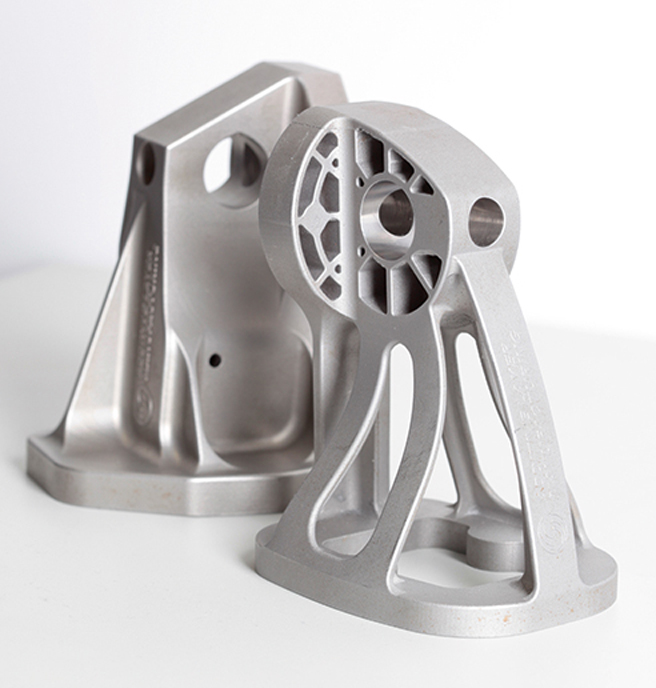
These will improve the consistency of the mechanical properties in any manufactured parts produced, and given the increasing popularity of Solukon systems within the aerospace industry, build on its offering to its aerospace customers. Protolabs has also invested in new post-processing equipment including a Solukon powder removal system and a new Ipsen vacuum heat-treat furnace. These bring Protolabs’ total DMLS machine count to more than 30 metal additive machines. In addition to the X Line 2000R, Protolabs has added four more GE Additive Concept Laser M2 printers to its portfolio, all of which are capable of manufacturing parts up to 9.8 in. The new agreement will see the Protolabs expand on its existing range of polymer and metal 3D printing equipment. The companies have a close business relationship, with Protolabs becoming a founding member of GE Additive’s Manufacturing Partner Network (MPN) two years ago. Launching its high requirements Direct Metal Laser Sintering (DMLS) offering last June, Protolabs purchased 25 Concept Laser Mlab and M2 machines from GE Additives.
#CONCEPT LASER XLINE ISO#
DMLS at Protolabs is also ISO 9001 and AS9100D-certified, providing industry-accepted quality standards from within the aerospace sector. Protolabs has heightened quality control measures, such as powder analysis, material traceability, and process validation for metal customers in response. Its emphasis is therefore on producing products that are ready for end-use production by utilizing secondary processes. This has been necessitated by a surge in customer demand for increasingly more complex components in high-requirement aerospace applications. The company has been focused on moving from prototyping into production for the last year. The headquarters will house at least 50 additional CNC machines and a further 20 additional injection molding presses, to continue its drive towards on-demand manufacturing. It’s currently redeveloping its Halesfield facility into a £5million European headquarters, which is set to be operational later this year. Headquartered in Minnesota, Protolabs offers digital manufacturing services from 12 locations around the world and continues to expand. Through our partnership with GE Additive, we are responding by scaling up the use of its cutting-edge equipment to further support our customers’ metal production needs,” said Vicki Holt, president, and CEO at Protolabs. “Our customers, especially in the aerospace industry, have told us they need the ability to create larger parts with complex geometries. The build volume of the metal laser melting machine offers significant applications for its growing customer base in the aerospace and automotive industries. Digital manufacturing company Protolabs plans to introduce GE Additive’s X-Line 2000R large-format 3D printers into its equipment portfolio in late summer 2020.īy expanding on its metal additive manufacturing capacity, Protolabs will enable its customers to access a new method of building large-format parts with complex geometries.
